E-Sharp News
July 2011
“ANCA’s TapX forms an essential part of our future growth at FEW” claims Rudie Odendaal, Factory Manager of French Engineering Works (FEW), who oversaw their first TapX machine installation in their Johannesburg based manufacturing plant in mid 2009. Now, with nearly two years of experience under their belt, FEW is satisfied with their decision to install the TapX in their production facility and have seen many positive results.
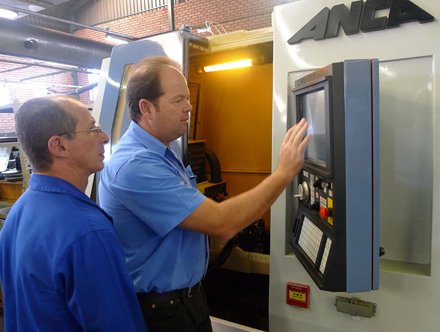
Rudy Odendaal, Factory Manager, operates the TapX with TapX Operator Paul Westphal
FEW’s path towards the TapX purchase started back at EMO in 2003, when they first saw the TapX grinding complete taps in a single set-up. This was an industry changing approach to tap production which had traditionally seen separate operations completed on multiple machines. Immediately, FEW recognised that the TapX would introduce new levels of flexibility to their production operations.
Odendaal explains, “Having an all-in-one tap grinding machine means we can dramatically reduce the total time to manufacture a batch of taps compared to the traditional process of multiple machines with multiple set-ups. Total set-up time for a batch of taps on the TapX is less than an hour, where it would have previously taken 3 or 4, were we to have done this same tap in the traditional multi-machine, multi-set-up way. This means we can turn around urgent orders to customers much more quickly. Our customers appreciate this level of responsiveness to their needs and are prepared to pay a premium for it.”
This is just the beginning of how the TapX is changing FEW’s business for the better. “Another area of improvement has been a reduction in numbers of reject tools and improvement in overall tool quality. Using the offline CIMulator3D to prove tool grinding programs before using them on the machine provides a tremendous advantage, but in addition, the machine itself has proven to be fantastically consistent in its grinding results. Usually on the TapX, we use only one tool for set-up before running a batch, and after that its production consistency is exceptional. On some tools that are particularly complex, or have tight tolerances, we might have previously endured scrap rates in excess of 10%, the TapX has no such problems.” The improved results are confirmed by FEW customers who have reported improved tool life and are now insisting that particular taps be ground on the TapX.
New special tap geometries manufactured on the TapX open up new markets for FEW
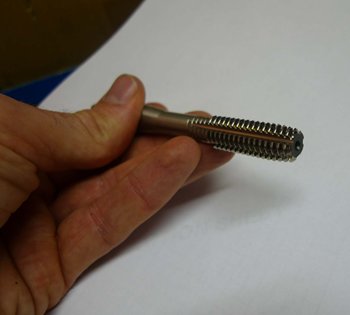
In addition to using the TapX in the manufacture of standard taps, FEW is now able to deliver new types of taps in previously inaccessible markets by grinding taps with geometries they previously were unable to consider. “Take for example, this special tap that features a unique thread profile (pictured below). We make this for an automotive manufacturer whose requirements for the tap design were unique to them.
Without the flexibility of the TapX software, and the machine itself, we probably would have walked away from such business in the past. Now we take it on and can command a premium for it. With this success behind us, we are now introducing new lines of special form taps and opening up new markets previously inaccessible to us.”
David Aldridge, FEW Managing Director, looks to the future of TapX for FEW. “Now with experience behind us, we can clearly see the benefits of the TapX to our business – it’s been a real success. Certainly we are now looking at further TapX machines in our future business so we can capitalise on the experience gained to date."
Download the TapX brochure here
6 July 2011