E-Sharp News
February 2024
Acutec added a couple ANCA grinders for in-house production of short run tools. As a result, the contract manufacturer has been able to save over 75% of the cost and can now produce a short batch of tools the same or next day rather than waiting 6-10 weeks for an outside supplier.
Acutec Precision Aerospace serves the commercial aircraft, defense, aerospace and power generation markets, supplying critical parts to systems providers for OEM platforms. Their products range from vibration damping and rotor components to engine, fuel system and air control, hydraulic actuation, avionics, landing gear and braking, rod ends, bearing and metal seals.
The company performs machining, EDM, metal finishing, welding and minor assembly operations at its three locations in Meadville and Saegertown, Pennsylvania as well as St. Stephen, South Carolina. Acutec is a contract manufacturer of CNC machined components and subassemblies, using precision- ground carbide end mills to machine materials on its nearly 300 machine tools and other equipment. A Certified Woman-Owned Small Business, Acutec carries AS9100D, ITAR and NADCAP certifications.
But Acutec faced a problem. There was a bottleneck in their tooling production.
As Tool Grinding Team Leader at the Saegertown facility, Chris Wagner, remarks, "We were having availability issues with our current cutting tool suppliers on quick-turnaround production order needs and wanted to bring the work in-house to have better control of quality and lead time." Sounds simple, right?
Not exactly. Acutec runs most of its tooling work in small batch orders of 3-10 pieces, with occasional needs for 150 pieces. The company produces form tools, broaches, lollipops, burrs, drills, step drills, reamers, boring bars, trepanning and engraving tools.
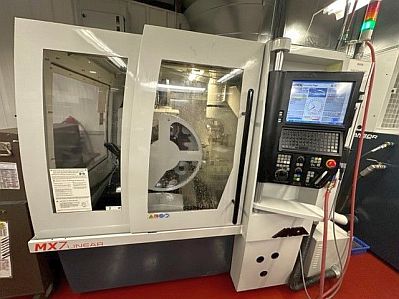
At an IMTS in Chicago, the company reviewed a number of tool grinder suppliers and saw the ANCA MX7 Linear machine. The MX7 Linear is a versatile CNC tool grinder designed for production grinding. It is built to meet the demands of high output, high-precision manufacturing. The powerful 38 kW (51HP) permanent magnet spindle provides high torque at lower RPM which is ideal for carbide grinding and a wide range of other applications.
At Acutec, 99% of their work is solid carbide with the remainder of the work involving the regrind of HSS cutting tools. After a demo at the ANCA facility in Wixom, Michigan, the machine was purchased, followed by a second machine, the FX5 Linear with a 19kW (25HP) spindle, AR300 Robot Automation and laser measurement. Tracking of the machines' performance in real time is made possible by the ANCA RedaX process monitoring software.
As Wagner explains, "We run the RN34.1 software package and use 3 Cimulators to create and save our programs. We have about 30 individual wheel packs preset for both machines to reduce setup time." He further notes that most of the jobs at Acutec require special tools, so knowing the ANCA software and machine capabilities has been his team's biggest advantage.
Acutec can now produce most of the tools necessary to run their more than 225 state-of-the-art CNC machines.
The ability to manipulate the software easily to create special operations for features that are specific to a tool is very helpful for Chris and his team, he adds. Wagner credits his previous 12 years as an applications engineer for ANCA and over 27 years of tool grinding experience with giving him and his team a real leg up on the design of tool geometry, but he notes the software is very intuitive and easy to learn. "The most helpful feature of the ANCA machines is the profile editor. I would say over 70% of the tools we grind utilize it," Wagner says.
The profile editor allows a designer to visualize and track the grinding wheel and tool profile machining operation for optimum efficiency in machine setup. Further, it offers the ability to combine multiple tools from a previous setup into a single, multi-step tool with easy modifications possible. As a result, according to Wagner, Acutec has been able to save over 75% of the cost by manufacturing its own tools vs purchasing them from an outside supplier. "We would often wait 6-10 weeks for a short batch of tools we can now produce next day or, when needed, same day to keep the spindles turning," he says proudly.
Wagner also highlights the ANCA special operations manager and scripting, which his team uses to create tool-specific operations as well as wizards to aid in the creation of tool files, quickly and consistently.
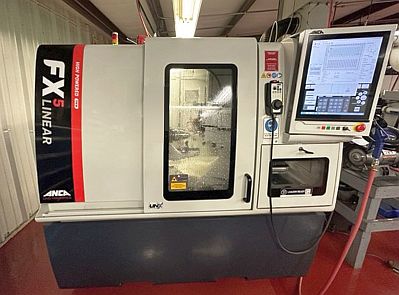
In the area of in-process tool measurement, Chris Wagner observes that, on longer run orders, the company has been able to utilize the laser measurement on the ANCA FX5 Linear machine to run up to 26 hours of unattended grinding.
Through the use of its ANCA machines, Acutec has achieved an ability to respond to down machine tools and change geometries on cutters without the long lead times from outside vendors. This ability to quickly respond to engineering changes has been recognized as a differentiator by customers on R&D collaborations.
Currently, Acutec performs 95% of its regrinding in-house and manufactures that same percentage of its special form tools. A consistent reduction of 50-75% in cost has been realized on the company's end mills and form cutters, translating into an annual tooling spend reduction of $200,000, according to the company.
Corporate accounting further reports the ROI on the ANCA machines has been under three years, plus the additional cost of equipment and labor were offset by the drastic reduction in spending with outside vendors for regrind and special form tools within one year.
18 January 2024